What is Porosity in Welding: Common Resources and Efficient Remedies
What is Porosity in Welding: Common Resources and Efficient Remedies
Blog Article
Porosity in Welding: Identifying Common Issues and Implementing Best Practices for Prevention
Porosity in welding is a prevalent problem that commonly goes undetected up until it triggers considerable issues with the integrity of welds. In this discussion, we will explore the key aspects contributing to porosity formation, examine its harmful impacts on weld efficiency, and talk about the ideal methods that can be taken on to minimize porosity occurrence in welding processes.
Common Causes of Porosity
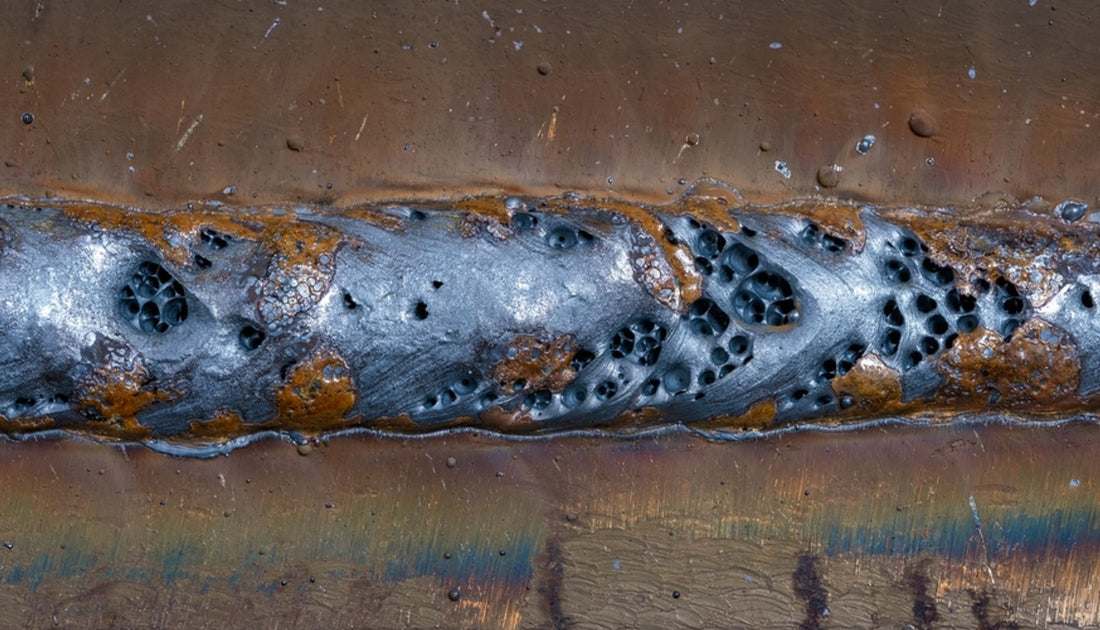
Making use of dirty or damp filler products can present pollutants into the weld, contributing to porosity problems. To alleviate these usual causes of porosity, comprehensive cleaning of base steels, correct protecting gas choice, and adherence to optimal welding parameters are crucial practices in accomplishing top notch, porosity-free welds.
Impact of Porosity on Weld High Quality

The presence of porosity in welding can dramatically jeopardize the structural stability and mechanical residential or commercial properties of bonded joints. Porosity creates voids within the weld metal, deteriorating its total toughness and load-bearing capability. These voids act as tension concentration factors, making the weld more susceptible to splitting and failure under used loads. Furthermore, porosity can lower the weld's resistance to rust and other environmental aspects, even more lessening its durability and efficiency.
Among the key consequences of porosity is a reduction in the weld's ductility and toughness. Welds with high porosity levels tend to show lower impact stamina and lowered ability to warp plastically prior to fracturing. This can be particularly concerning in applications where the bonded elements are subjected to vibrant or cyclic loading conditions. Moreover, porosity can hinder the weld's ability to properly transfer pressures, resulting in premature weld failing and possible safety and security risks in essential frameworks.
Ideal Practices for Porosity Avoidance
To enhance the structural stability and top quality of welded joints, what particular procedures can be carried out to reduce the occurrence of porosity during the welding procedure? Utilizing the right welding method for the particular product being welded, such as readjusting the welding angle and gun setting, can even more stop porosity. Routine assessment of welds and prompt remediation of any problems identified during the welding process are vital techniques to prevent porosity and generate top quality welds.
Importance of Proper Welding Techniques
Carrying out appropriate welding strategies is vital in making certain the architectural stability and quality of bonded joints, constructing upon the structure of efficient porosity prevention procedures. Excessive warm can lead to boosted porosity due to the entrapment of gases in the weld pool. Furthermore, using the appropriate welding parameters, such as voltage, present, and take a trip speed, is vital for accomplishing sound welds with marginal porosity.
Furthermore, the option of welding procedure, whether it be MIG, TIG, or stick welding, need to align with the specific needs of the job see this site to make sure optimal outcomes. Proper cleansing and preparation of the base discover this metal, in addition to picking the best filler product, are additionally necessary parts of proficient welding methods. By adhering to these ideal practices, welders can lessen the risk of porosity development and produce top quality, structurally sound welds.

Testing and Quality Assurance Actions
Quality assurance actions play an important duty in verifying the stability and dependability of bonded joints. Evaluating treatments are important to spot and prevent porosity in welding, making certain the toughness and durability of the end product. Non-destructive screening methods such as ultrasonic screening, radiographic screening, and aesthetic examination are commonly employed to recognize possible problems like porosity. These methods enable the evaluation of weld quality without jeopardizing the honesty of the joint. What is Porosity.
Carrying out pre-weld and post-weld examinations is likewise vital in preserving quality control standards. Pre-weld inspections include verifying the materials, devices settings, and sanitation of the workplace to stop contamination. Post-weld assessments, on the various other hand, analyze the final weld for any kind of issues, consisting of porosity, and verify that it fulfills specified criteria. Executing a detailed quality control strategy that consists of comprehensive testing treatments and assessments is vital to reducing porosity problems that site and guaranteeing the overall quality of bonded joints.
Conclusion
Finally, porosity in welding can be a common problem that impacts the top quality of welds. By identifying the common causes of porosity and executing finest practices for prevention, such as correct welding methods and testing actions, welders can make sure premium quality and reliable welds. It is important to prioritize prevention techniques to minimize the incident of porosity and keep the honesty of welded frameworks.
Report this page